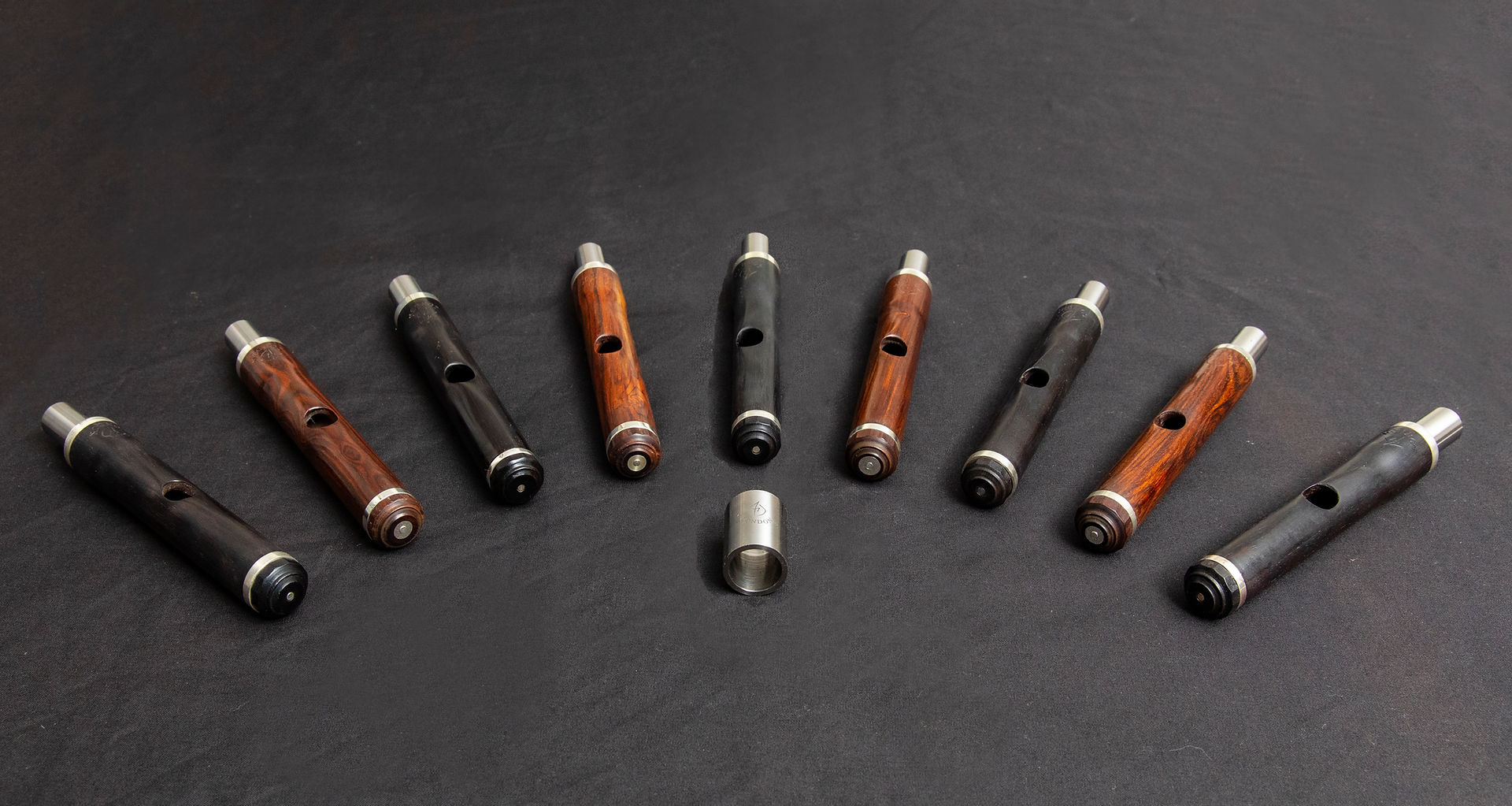
PICCOLO HEADJOINT MAKER
FLUTE/PICCOLO REPAIRER

~TESTIMONIALS~
"I wish I had this headjoint when I played with the Berlin Philharmonic Orchestra."
"I was always moving the cork position to get the richest and best sound... With this new mechanism, the ability to move the cork assembly has been made easy"
"This is simply the best headjoint I have ever played."
RAINER LAFIN / HEADJOINT MAKER
“The lower register has a wonderful resonance and depth of colour, but I particularly like the singing quality of the upper register."
"..an amazing stability throughout which is a game changer, especially in the low register"
KATHLEEN STEVENSON / BBC SYMPHONY ORCHESTRA / PRINCIPAL PICCOLO

A little bit about Me
I began playing piano at the age of 6 and flute age 8. Music formed part of my early childhood and followed me through school and finally college where I was taught by some of the finest players in the country.
I entered the profession aged 21 playing with the BBC Scottish Symphony Orchestra and Royal Scottish National Orchestra and Scottish Ballet.
I moved to London in 1994 and established my career there, becoming one of the top freelancers on flute and piccolo. I trialled for principal piccolo with the London Symphony Orchestra, Royal Opera House and almost all of the other orchestras in England, branching out to play ethnic flutes for various West End shows and sessions.
I began making piccolo headoints after finally taking a piece of Pink Ivory that I had been given 15 years previously, to a flute maker, restorer and flute historian and someone who has become a dear friend and advisor to me, Robert Bigio. Robert gave me a day of instruction and guided me towards the path of buying machinery and tools to ply a craft I knew little about but had been using almost my entire life. That day I made two headjoints. And so began my journey.
I applied my practical knowledge to making headjoints and utilised my vast experience as a player to work out solutions to make something that made the challenges of playing the piccolo a little easier, or at the very least more pleasurable.
Being a professional flautist gives me a great advantage in making a product that gives my customers that edge to their playing experience.
I believe that we are actually as good as the instruments we play. I sometimes wish I had played on a top end instrument when I went to college but money was never freely available, so I learned on the best my parents could afford and saved so that one day I could step up to the next level. Now after so many years in the profession I play on the best instruments but also now make headjoints that further my abilities.
How lucky am I.

Working with wood is a very organic process.
All my headjoints are completely hand made.
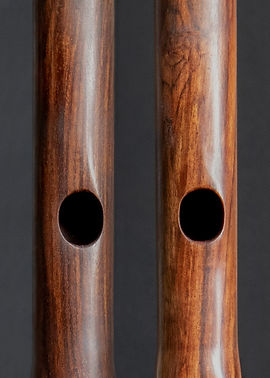
Sometimes a measurement will change by the thickness of 0.01mm due to sanding or polishing.

Add to this the individual grain, density and character of the wood which results in no two headjoints being the same.

My Process
TYPES OF WOOD
I CURRENTLY USE
Hopefully by the end of the current lockdown my headjoints can also be tried and purchased at the following flute shops:
The wood I purchase comes from ethical and sustainable sources. I carry certificates of traceability for these purchases.

MATURING AND
SOURCING OF THE WOOD
After the process of turning and boring, most of my wood is left for 1-2 years in a controlled environment before it is finished.
This allows the wood to settle.
The cocus wood I have comes from stock originally owned by Rudall Carte. The rough turned and bored wood could potentially be between 70 and 150 years old.
There are only 16 of these headjoints now left and so far these ones are showing amazing richness of tone and colour.


